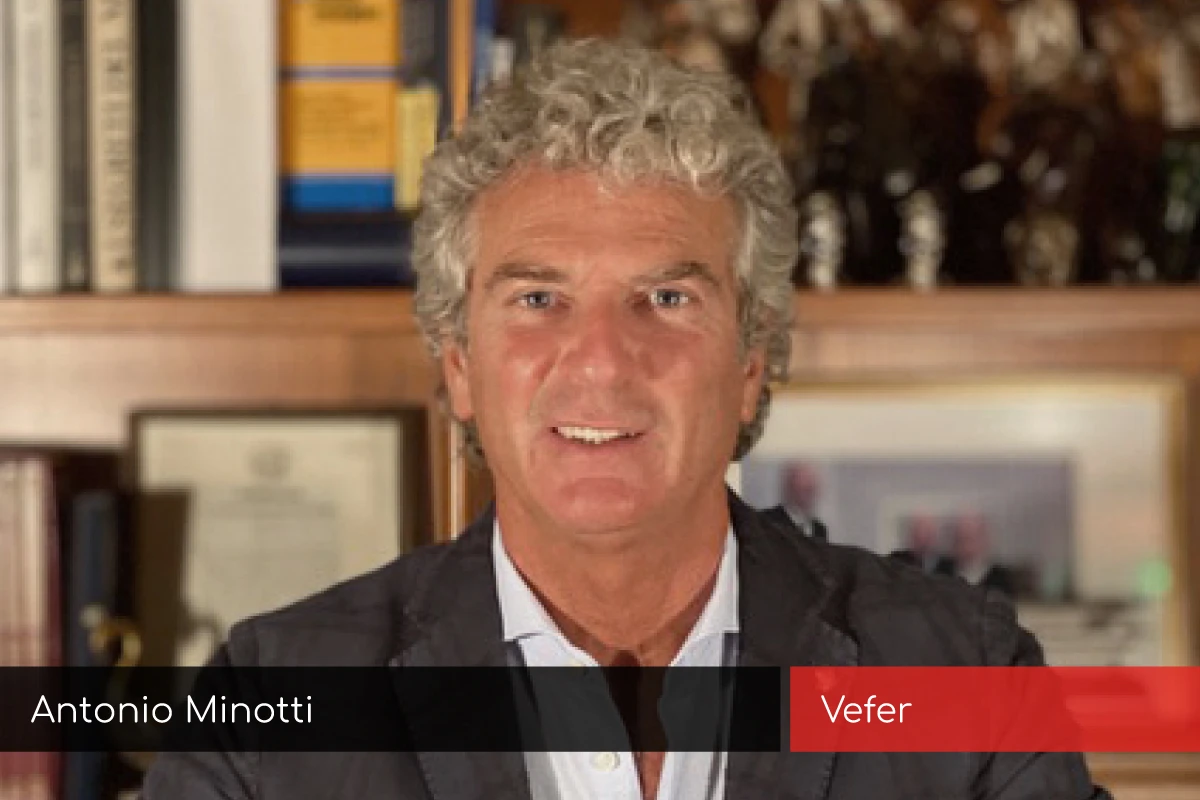
Forschung, Respekt und Innovation sind das "Leitmotiv" von Vefer, einer unternehmerischen Realität, die in Italien und Europa bei der Herstellung von flexiblen Polyurethanen für die Blockierung führend ist.
Stets aufmerksam auf die vielfältigen Bedürfnisse des Marktes, setzt das Unternehmen mit Sitz in Lissone seine Forschungs- und Innovationspolitik fort, die auf die Herstellung von immer leistungsfähigeren, komfortableren und nachhaltigeren Polyurethanen abzielt.
Gerade über nachhaltige Produkte, die Kreislaufwirtschaft, den reduzierten Verbrauch von Rohstoffen und die Nachhaltigkeit haben wir mit Antonio Minotti, dem Geschäftsführer von Vefer, gesprochen.
Nachhaltigkeit wird heute als eine große Chance für Unternehmen angesehen. Wie drückt sich diese Sorge um die Umwelt in Ihrem Unternehmen aus?
Vefer war schon immer für das Thema Nachhaltigkeit sensibilisiert, und heute stehen wir noch mehr in der ersten Reihe, um unseren Beitrag zu leisten.
Die Produktion wird so gesteuert, dass der Verbrauch natürlicher Ressourcen minimiert wird, die Verschmutzung und die negativen Auswirkungen auf die Umwelt so gering wie möglich gehalten werden und faire Arbeitsbedingungen für die Mitarbeiter gewährleistet sind.
Vefer, seit jeher ein Vorreiter in Sachen Umweltschutz, war der erste Hersteller von Polyurethanschaumstoffen in Europa, der Schaumstoffe mit Rohstoffen aus erneuerbaren Quellen, aus Ricinolsäure gewonnenen Polyolen, produzierte. Daraus ist die Biogreen®-Schaumstoffklasse entstanden.

Biogreen® ist ein Produkt, das aus natürlichen, nicht kontaminierenden, nachwachsenden Rohstoffen hergestellt wird.
Für die Herstellung aller Heftklammern des Unternehmens werden Produktionsabfälle aus der Schaumstoffverarbeitung verwendet, d.h. zweiter Rohstoff, und es wird kein neuer Schaumstoff verwendet. Darüber hinaus werden alle Produktionsabfälle des Unternehmens, die nicht für die Lieferung von Polstermöbelklammern verwendet werden, in gepressten Verpackungen zur Wiederverwendung im Bereich von Teppichen und Füllstoffen in schalldämmenden Asphalten verkauft.
Vefer hat vor kurzem eine Zusammenarbeit mit Repsol, einem führenden Hersteller von Polyolen, dem Rohstoff für die Herstellung von Polyurethan, begonnen, um Schaumstoffe zu entwickeln, die aus Polyolen hergestellt werden, die aus dem Recycling von gebrauchten Polyurethanschaum-Matratzen stammen, wodurch die CIRCULARREFOAM®-Klasse von Polyurethanen entsteht.
Diese Produktion in Zusammenarbeit mit der bedeutenden OETI-Zertifizierungsstelle in Wien führte zum ersten Qualitätszertifikat für Schaumstoffe, die auf kreisförmige Weise hergestellt werden.

CIRCULARREFOAM® umweltfreundlicher Polyurethanschaum aus 15% recycelten Polyolen
Hat Vefer Pläne für Effizienz und Reduzierung des Rohstoffverbrauchs?
Vefer hat in seinem Industrieplan die Absicht formuliert, das als Lean Plastic bekannte Produktionsmodell zu übernehmen, das vom Toyota-System abgeleitet ist und speziell auf die Welt der Kunststoffe angewendet wird.
Der Plan sieht vor, ein Unternehmen zu finden, das dieses Projekt in einer ersten Prüfphase unterstützt, um Verbesserungsmöglichkeiten aufzuzeigen und anschließend die notwendigen Maßnahmen zur Umsetzung des so genannten "Vefer-Produktionssystems" durchzuführen.
Der Industrieplan sieht eine Effizienzsteigerung der Lay-Outs der Abteilungen aus einer Lean-Perspektive, eine Reduzierung der Verschwendung und eine Verbesserung der Intralogistik vor, wodurch der Wertfluss entlang der gesamten Unternehmensachse gewährleistet wird.
Ein weiteres Thema sind die Rohstoffe, da sie an genaue Rezepturen gebunden sind, um Schaumstoffe mit vordefinierten technischen Eigenschaften zu erhalten.
Zur Verringerung des Rohstoffverbrauchs hat Vefer einen Geschäftsplan mit einem diversifizierten Ansatz verabschiedet: die Verwendung von Polyolen, die aus gebrauchten Matratzen gewonnen werden (CIRCULARREFOAM®-Schaumstoffe), ein laufendes Projekt mit einer europäischen Kooperation und die Verringerung der internen Spezialchargen (Produkte zweiter Wahl).
Die Verringerung von zweitklassigen Produkten hat eine doppelte Wirkung, zum einen eine Verringerung des Rohstoffverbrauchs, zum anderen Energieeinsparungen zur Vermeidung einer erneuten Verarbeitung und eines weiteren innerbetrieblichen Transports mit einer daraus resultierenden Zunahme der Formabfälle.